One small crack in an aircraft component can lead to major problems. The cracks can grow fast and damage metal components to the point of failure, but they are often hard to detect.
In an effort to stop this problem as it starts, the Defense Advanced Research Projects Agency recently awarded UCF aerospace engineering Assistant Professor Ranajay Ghosh a $100,000 grant.
Ghosh and his co-principal investigator, aerospace engineering Professor Seetha Raghavan, will develop sophisticated computer models to pinpoint the initial stages of stress-corrosion cracking.
Stress-corrosion cracking occurs when stress and corrosion create cracks in metal aircraft components such as engines, wings and landing gears. These are also the areas that can quickly lead to catastrophic failure.
“These cracks often initiate at sub-micron or even nanometer length scales and thus can stay undetected for quite some time,” Ghosh says. “By the time the cracks are visible, damage is already well underway.”
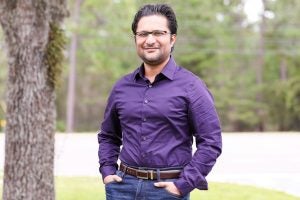
Stress-corrosion cracking is observed in lightweight aerospace materials, particularly aluminum. Although it’s a serious and potentially life-threatening issue, researchers don’t know exactly how it starts. That’s a mystery Ghosh intends to solve with state-of-the-art computer models.
Once the computer models are developed, they could lead to the creation of physical models, and ultimately, early stress-corrosion cracking detection and warning systems that could isolate damaged areas. They could also lead to the design of materials and coatings that are resistant to stress-corrosion cracking.
To create the models, he’ll use powerful computers to solve and analyze complex scientific equations.
“These equations will be analyzed in great detail and compared with sophisticated X-ray techniques to improve accuracy,” Ghosh says. “The resulting model will then be used to create a computer simulation of crack initiations under some of the common conditions that are already known to cause stress corrosion cracking.”
Because the rates of corrosion and oxidation occur rapidly at the microscopic level, Ghosh will use data from synchrotron X-rays, which are extremely powerful light beams created in a particle accelerator. The X-ray data will be captured at Argonne National Laboratory in Illinois using advanced instrumentation and measurement techniques developed by Raghavan during the past decade. The X-rays will allow them to observe the micro structural degradation and oxidation of stress-corrosion cracking in real time, and that information will be fed into the computer models.
“We’re using a state-of the art, in situ sample environment design to attack an age-old problem,” Raghavan said.
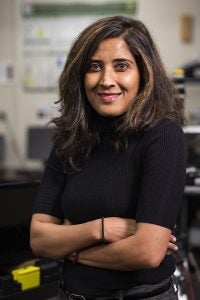
This project is funded under DARPA’s Polyplexus pilot program, a derivative of the organization’s new collaborative platform called Polyplexus. This public social network, which launched in 2019, allows members of the research community to connect with DARPA’s program managers to explore potential opportunities for research.
Ghosh joined UCF in 2016 as an assistant professor in the Department of Mechanical and Aerospace Engineering and is a researcher with MAE’s Center for Advanced Turbomachinery and Energy Research. He manages the Complex Structures and Mechanics of Solids Laboratory, better known as the COSMOS Lab, where he and his team fabricate and design novel materials with the aid of computer models and experiments. He earned his doctorate in mechanical and aerospace engineering from Cornell University in 2010 and is a recipient of the National Science Foundation CAREER Award.
Raghavan is a professor and the program director for the aerospace engineering program at UCF. She also leads the Raghavan Research Group for Aerostructures and is a researcher with MAE’s Center for Advanced Turbomachinery and Energy Research. She earned her doctorate in aeronautics and astronautics from Purdue University and has won numerous awards for research and teaching, including the Aerospace Educator Award from Women in Aerospace.